Condensador Ceramico
El Condensador Cerámico es un componente electrónico pasivo que es capaz de almacenar una carga eléctrica, se comporta como un filtro que bloquea la corriente directa y permite que la corriente alterna fluya sin ningún problema.
Este tipo de condensador está compuesto de dos superficies conductoras llamadas electrodos, separadas por un aislante el cual es llamado “dieléctrico”.
Las altas constantes dieléctricas características de las cerámicas,
permiten amplias posibilidades de diseño mecánico y eléctrico.
A diferencia de algunos condensadores, el condensador de cerámica no está polarizado, lo cual significa que los dos electrodos no están cargados activa y negativamente; y utiliza capas de metal y cerámica como dieléctricos.
El dieléctrico utilizado por este tipo de Condensador es la cerámica, siendo el material más utilizado para su fabricación el dióxido de titanio. Este material le da al condensador grandes inestabilidades, por lo que en base al material, se pueden diferenciar dos grupos.
- Grupo I: Caracterizado por una alta estabilidad, con un coeficiente de temperatura bueno y casi constante.
- Grupo II: Su coeficiente de temperatura no está definido y presenta características no lineales, su capacidad varía considerablemente con la temperatura, la tensión y el tiempo de funcionamiento.
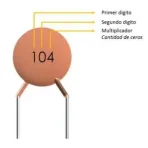
Clasificación de los Condensadores Cerámicos
Cerámicos de clase I
Los condensadores cerámicos de clase 1 son condensadores precisos que compensan la temperatura. Ofrecen la mayor estabilidad de tensión, temperatura y, hasta cierto punto, frecuencia. Tienen las pérdidas más bajas y, por tanto, son especialmente adecuados para aplicaciones de circuitos resonantes en las que la estabilidad es esencial o en las que se requiere un coeficiente de temperatura definido con precisión, por ejemplo, para compensar los efectos de la temperatura en un circuito.
Los materiales básicos de los condensadores cerámicos de clase 1 se componen de una mezcla de gránulos finamente molidos de materiales paraeléctricos como el dióxido de titanio (TiO2), modificados por aditivos de zinc, circonio, niobio, magnesio, tántalo, cobalto y estroncio, que son necesarios para conseguir las características lineales deseadas del condensador.
Se utilizan en los siguientes circuitos:
- Circuitos de resonancias
- Altas frecuencias.
- Acoplamiento.
- Dieléctricos de temperatura compensada.
- Estabilidad dieléctrica.
- Otras aplicaciones.
Cerámicos de clase II
Los condensadores cerámicos de clase 2 tienen un dieléctrico con una alta permitividad y, por tanto, una mejor eficiencia volumétrica que los condensadores de clase 1, pero menor precisión y estabilidad. El dieléctrico cerámico se caracteriza por un cambio no lineal de la capacitancia a lo largo del intervalo de temperaturas.
El valor de la capacitancia también depende de la tensión aplicada. Son adecuados para aplicaciones de derivación, acoplamiento y desacoplamiento o para circuitos de discriminación de frecuencias en los que las bajas pérdidas y la alta estabilidad de la capacitancia son menos importantes.
Los condensadores de clase 2 están fabricados con materiales ferroeléctricos como el titanato de bario (BaTiO3) y aditivos adecuados como silicato de aluminio, silicato de magnesio y óxido de aluminio. Estas cerámicas tienen una permitividad muy alta (de 200 a 14.000), lo que permite un campo eléctrico extremo y, por tanto, capacitancia dentro de paquetes relativamente pequeños:
los condensadores de clase 2 son significativamente más pequeños que los de clase 1 comparables. Sin embargo, la permitividad no es lineal con respecto a la intensidad de campo, lo que significa que la capacitancia varía significativamente a medida que aumenta la tensión en los terminales. Los condensadores de clase 2 también presentan una baja estabilidad térmica y envejecen con el tiempo.
Debido a estas características, los condensadores de clase 2 se utilizan normalmente en aplicaciones en las que sólo se requiere un valor mínimo de capacitancia (en lugar de un valor exacto), como la amortiguación/filtrado de entradas y salidas de fuentes de alimentación y el acoplamiento de señales eléctricas.
Los condensadores de clase 2 se etiquetan según el cambio de capacitancia a lo largo del intervalo de temperatura. La clasificación más utilizada se basa en la norma EIA RS-198 y utiliza un código de tres dígitos.
El primer carácter, una letra, denota la temperatura de funcionamiento más fría; el segundo carácter, un número, denota la temperatura más caliente; y el tercer carácter, otra letra, denota el cambio de capacitancia máximo permitido en todo el rango de temperatura especificado del condensador:
Sistema de codificación según EIA RS-198 para algunos rangos de temperatura y cambio inherente de capacitancia
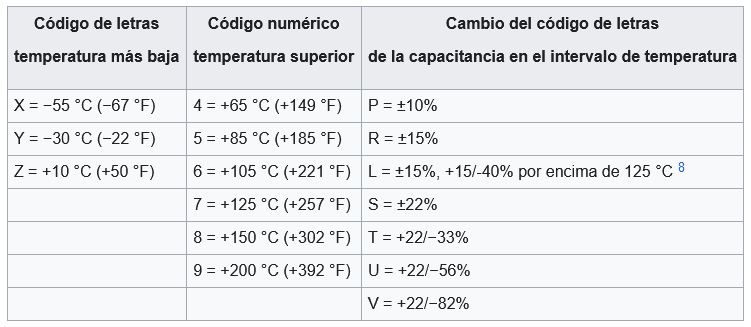
Cerámicos de clase III
Este tipo de condensador son de propósito general.
Su cualidad es la baja resistividad que ofrece y que esta por debajo de los 10W/-cm, esto se consigue sometido el disco cerámico aislante a un tratamiento de calor en una atmósfera reducida.
Esta clase de condensadores son utilizados en circuitos de acoplamiento y supresor de interferencia.
Construcción y estilos
Los condensadores cerámicos se componen de una mezcla de gránulos finamente molidos de materiales paraeléctricos o ferroeléctricos, mezclados adecuadamente con otros materiales para conseguir las características deseadas.
A partir de estas mezclas de polvos, la cerámica se sinteriza a altas temperaturas. La cerámica forma el dieléctrico y sirve de soporte para los electrodos metálicos. El grosor mínimo de la capa dieléctrica, que hoy en día (2013) para los condensadores de baja tensión está en el rango de tamaño de 0,5 micrómetros, está limitado a la baja por el tamaño de grano del polvo cerámico. El grosor del dieléctrico para condensadores con tensiones más altas viene determinado por la rigidez dieléctrica del condensador deseado.
Los electrodos del condensador se depositan sobre la capa cerámica mediante metalización. En los MLCC se apilan capas cerámicas metalizadas alternas una sobre otra. La metalización sobresaliente de los electrodos a ambos lados del cuerpo se conecta con el terminal de contacto. Un revestimiento de laca o cerámica protege el condensador contra la humedad y otras influencias ambientales.
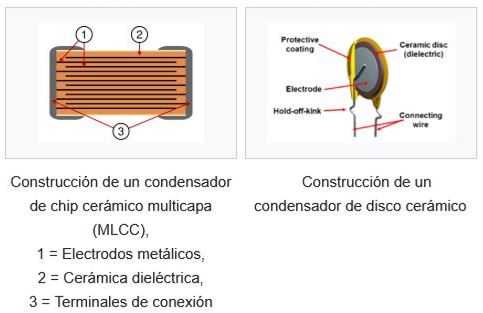
Los condensadores cerámicos tienen varias formas y estilos. Algunos de los más comunes son:
- Condensador de chip cerámico multicapa (MLCC), bloque rectangular, para montaje en superficie.
- Condensador de disco cerámico, disco de una capa, recubierto de resina, con conductores de orificio pasante
- Condensador cerámico de paso, utilizado para derivación en circuitos de alta frecuencia. Forma de tubo, metalización interior en contacto con un conductor, metalización exterior para soldar
- Condensadores cerámicos de potencia, cuerpos cerámicos más grandes de diferentes formas para aplicaciones de alta tensión
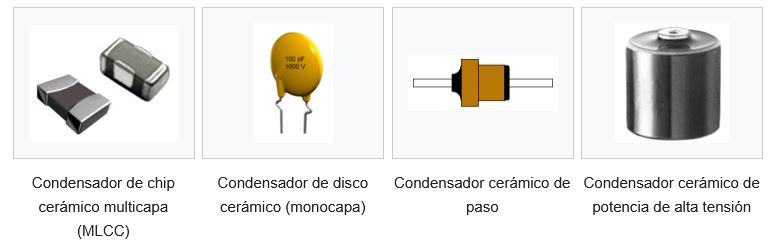
Condensadores cerámicos multicapa (MLCC)
Se puede considerar que un MLCC está formado por muchos condensadores de una sola capa apilados en un solo paquete.
El material de partida de todos los chips MLCC es una mezcla de gránulos finamente molidos de materias primas paraeléctricas o ferroeléctricas, modificadas por aditivos determinados con precisión. La composición de la mezcla y el tamaño de las partículas de polvo, tan pequeñas como 10nm, reflejan la experiencia del fabricante.
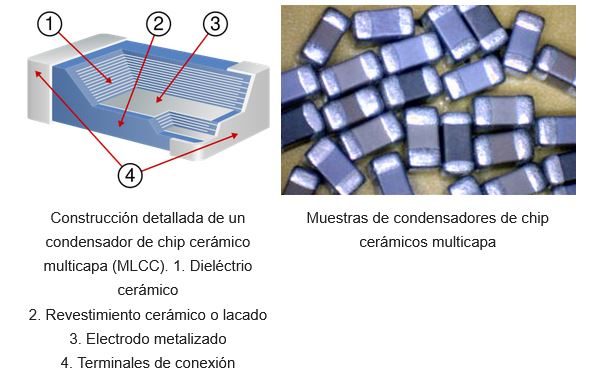
A partir de una suspensión del polvo con un aglutinante adecuado, se moldea una fina lámina cerámica.
Los rollos de lámina se cortan en hojas del mismo tamaño, que se serigrafían con una capa de pasta metálica, que se convertirá en los electrodos. En un proceso automatizado, estas láminas se apilan en el número de capas necesario y se solidifican por presión. Además de la permitividad relativa, el tamaño y el número de capas determinan el valor de capacitancia posterior.
Los electrodos se apilan en una disposición alterna ligeramente desplazada respecto a las capas contiguas, de modo que cada uno de ellos pueda conectarse posteriormente en el lado desplazado, uno a la izquierda y otro a la derecha. La pila de capas se prensa y luego se corta en componentes individuales. Se requiere una gran precisión mecánica, por ejemplo, para producir una pila de 500 o más capas del tamaño “0201” (0,5 mm × 0,3 mm).
Tras el corte, se quema el aglutinante de la pila. A continuación, se sinteriza a temperaturas comprendidas entre 1.200 y 1.450 °C, con lo que se obtiene la estructura final, principalmente cristalina. Este proceso de quemado crea las propiedades dieléctricas deseadas. A continuación, se limpian y se metalizan las dos superficies de los extremos.
Mediante la metalización, los extremos y los electrodos interiores se conectan en paralelo y el condensador obtiene sus terminales. Por último, cada condensador se prueba eléctricamente para garantizar su funcionalidad y rendimiento adecuado, y se embala en una bobina de cinta.
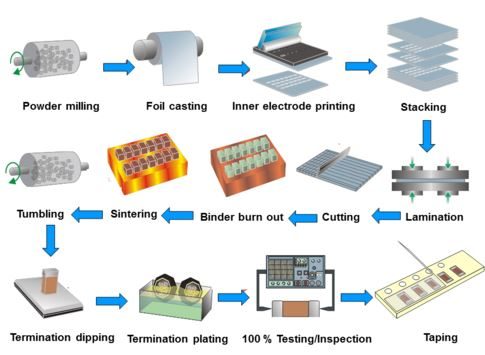